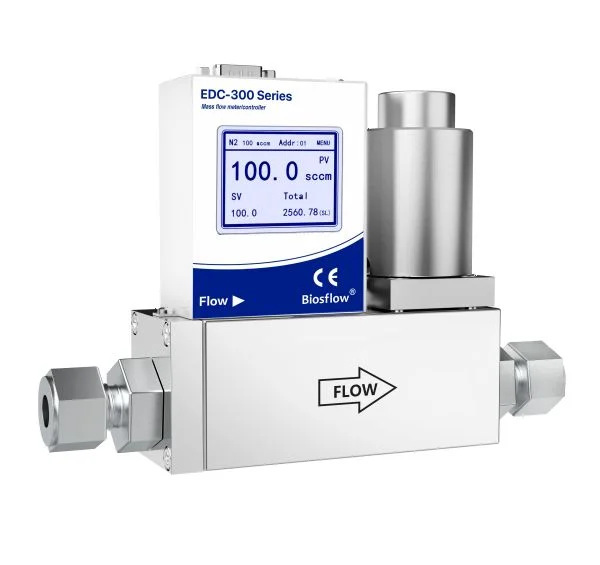
EDC-300 Series Mass Flow Controller and Meters
- Full Scale Flow Range(3sccm-1000slm)
- Maximum working pressure up to 1500 Psi
- High precision measurement and control
- High pressure differential adaptability
- Unaffected by temperature and pressure
- Quick response, high repeatability
- Digital communication, compatible with analog communication
- Optional real-time display with LCD screen
Description of EDC-300 Series Mass Flow Controller and Meters
EDC-300 series is a new generation of MFC/MFM(Mass Flow Controller/Mass Flow Metes) with newly designed.It adopts many world-leading fluid measurement and control technologies. On the basis of capillary thermal temperature difference sensor, it introduces advanced “Automatic temperature difference balancing technology” to ensure the extraordinary stability, linearity and dynamic response characteristics of the sensor. The substrate is made of 316L stainless steel, suitable for toxic and corrosive gases, the maximum working pressure can reach 1500 Psi, and the maximum flow rate can reach 1000 SLM. Newly designed digital measurement control circuit, multiple communication protocols for digital IO, compatible with analog communication, optional LCD version, convenient on-site operation display. The excellent performance of the EDC series is the best partner for high-quality applications.
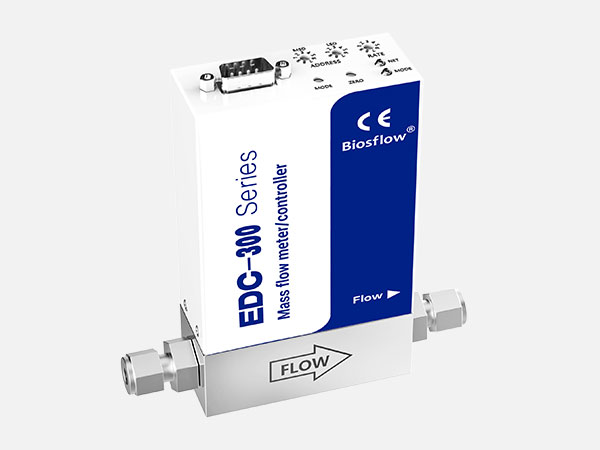
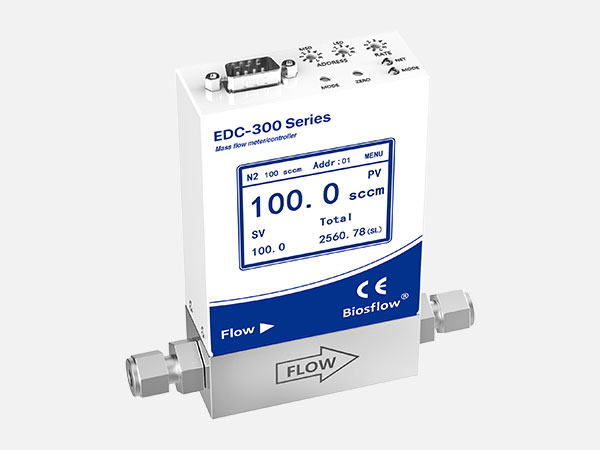
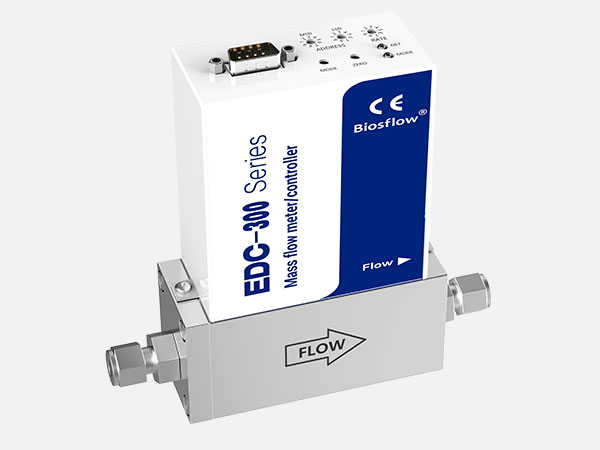
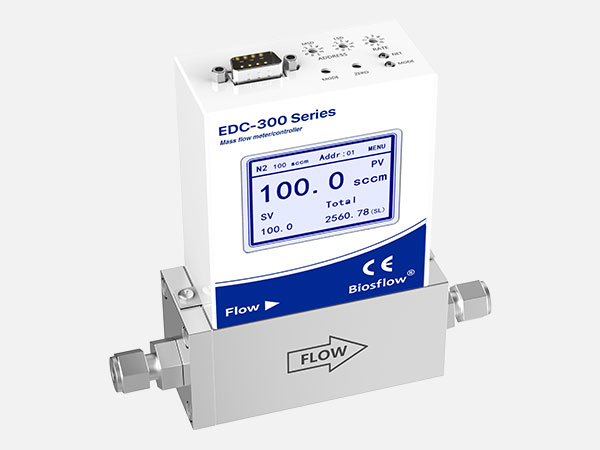
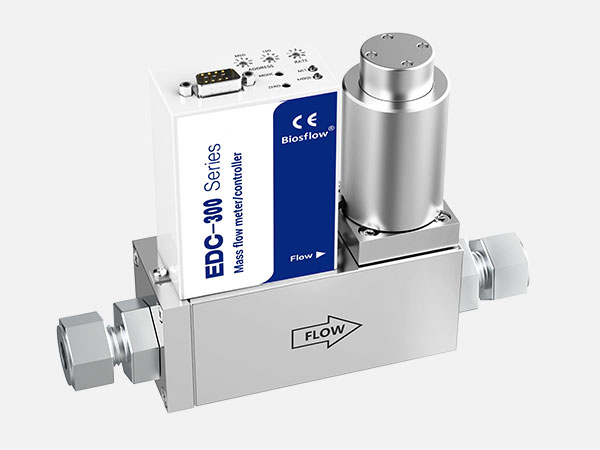
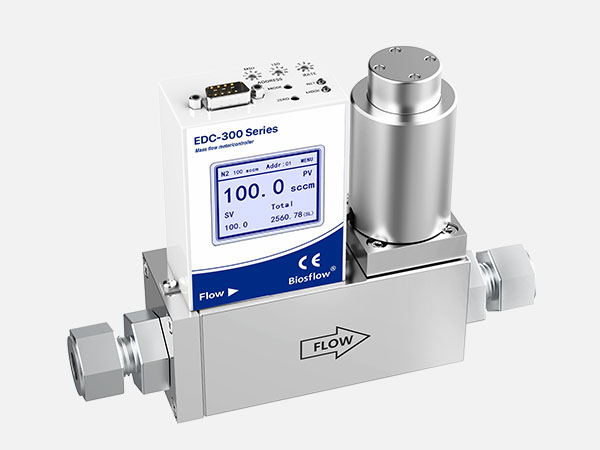
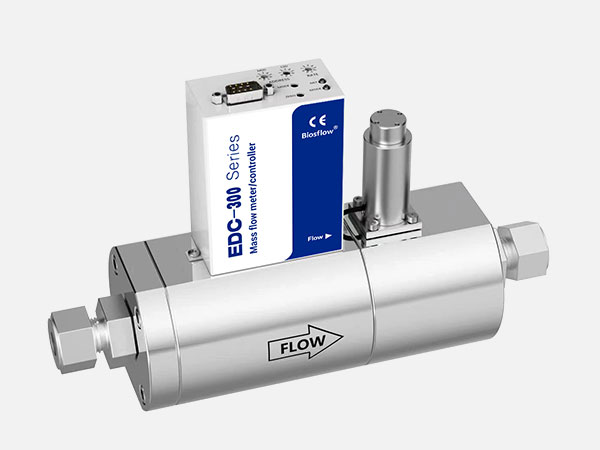
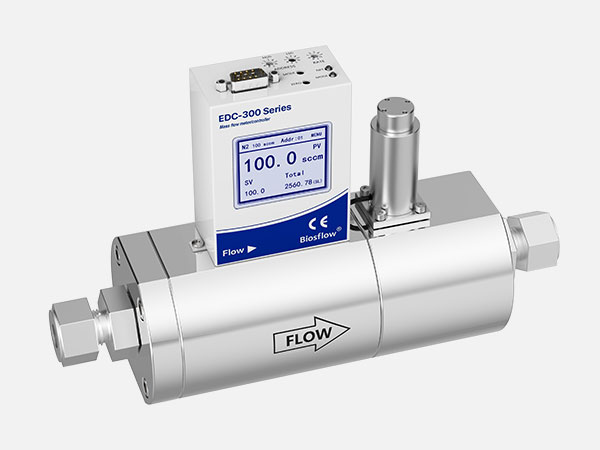
Biosflows EDC-300 Mass Flow Controller and Meters Principle
Sensor Schematic
The core sensor of the thermal mass flow meter (MFM) is the principle of capillary thermal temperature difference, which is composed of a stainless steel capillary with a thermal sensor and a heating element. A part of the gas flows through the bypass sensor and is heated by the heating element. The gas flow causes an asymmetrical temperature distribution, which is proportional to the mass flow through the sensor.
MFC Structure Diagram
The main flow channel of the thermal mass flow controller (MFC) is perfectly shunted by the laminar flow element, so that the output of the sensor has a linear relationship with the total mass flow. The output signal of the sensor is amplified and compared with the signal set by the user, the opening of the solenoid valve is controlled by the PID algorithm, the flow is adjusted, and the closed-loop control of the mass flow is realized.
Biosflows EDC-300 Mass Flow Controller and Meters Technical Parameters
Performance | |
---|---|
Flow Accuracy | ±0.8% R.D and±0.2% F.S; ±1% R.D and ±0.5% F.S(>100 SLM) |
Repeatability | ±0.2% F.S |
Control Range | 1~100% F.S |
Response Time | <1s |
Temperature Coefficient | Zero: <0.05% of F.S./℃. Span: <0.1% of S.P. /℃ |
Pressure Coefficient | 0.2% of S.P. / Bar |
Operating Temperature | 0~50℃ |
Leak Rate | 1x10-9 atm. cc/sec He |
Preheat Time | 5 min accuracy to ±2% F.S (30 min to achieve the best accuracy) |
Power Supply | +15~24 V DC |
Maximum Power Consumption | 10W (MFC); 3W (MFM) |
Digital Communication | RS-485(Modbus Rtu protocol) |
Analog Communication | 0~5 V / 4~20mA |
Electrical Interface | 9-Pin D-connector (Male) |
Valve Type | Normally closed (MFM meaningless) |
Substrate Material | 316L stainless steel |
Sealing Material | Fluorine rubber, EPDM rubber, nitrile rubber |
Process connections | Tube/VCR Fittings |
EDC-300 Series Mass Flow Controller and Meters Size and Weight
Model | A | B | C | D | H | E | F | G | M | Weight |
---|---|---|---|---|---|---|---|---|---|---|
EDC-310/1/5/6 | 76 | 124 | 13 | 31 | 125 | 56 | 17 | 10 | M4 | 0.6 |
EDC-320/1/5/6 | 76 | 124 | 13 | 31 | 125 | 56 | 17 | 10 | M4 | 0.6 |
EDC-330/1/5/6 | 98.5 | 147 | 17 | 40 | 135 | 66.5 | 20 | 16 | M4 | 0.8 |
EDC-340/1/5/6 | 98.5 | 147 | 17 | 40 | 135 | 66.5 | 20 | 16 | M4 | 1 |
EDC-350/1/5/6 | 132 | 208 | 22 | 50 | 150 | 96.5 | 30 | 16 | M4 | 1.5 |
EDC-360/1/5/6 | 185 | 260 | 37 | 85 | 170 | 170 | 30 | 7.5 | M6 | 2.5 |
Features of EDC-300 Series Mass Flow Controller and Meters
The influence of temperature and pressure changes is small, accurate temperature and pressure correction, high linearity, can provide excellent signal-to-noise ratio performance to improve measurement and control accuracy long-term zero point stability.
The new microelectronic chip energy-saving technology and innovative multi-level control loop bring super dynamic characteristics. Control performance is adaptive, allowing quick response to setpoint changes without overshoot. Welcome to inquiry in Biosflows.
There are various input/output options of EDC-300 Series Mass Flow Controller and Meters. In addition to various analog signals and standard RS232 communication options, valve cleaning/closing and valve analog output. Multiple fieldbus optional. Get free quotation here.
The flow range can be from 3sccm all the way to 1000 SLM, the working pressure is up to 500 psi/100 bar, and the flow measurement and control can be performed under the extremely high pressure difference between upstream and downstream from 6 bar to 70 bar.
Choose one device platform to meet the needs of different gases and flow ranges, store and pre-set multiple gas calibration information, so choose our EDC-300 Series Mass Flow Controller, users can easily switch to different gases and ranges with just one device .
Aplication of EDC-300 Series Mass Flow Controller and Meters
Gas Control During Fiber Fabrication
Optical fiber preform equipment, optical fiber drawing, and ribbon optical fiber preparation in the optical fiber industry. During the fiber drawing process, the composition and flow of the atmosphere need to be controlled to ensure the quality and performance of the fiber. Need to supply a certain amount of gas, such as protective gas, dry gas, etc. Optical fiber drawing MFC is used to control the flow rate and mixing ratio of the gas to provide the correct atmosphere environment. To ensure that the optical fiber preparation process is stable and repeatable.
Bioreactor Gas Flow Control
Accurate, repeatable and stable airflow is critical to a reliable biological growth process.Especially in R&D environments, a large range of gas flow variations is required to study optimal growth conditions. Benchtop bioreactors require compact gas flow instrumentation. For manufacturers who build bioreactors to customer specifications, there is a need to reduce the number of variations of various flow instrumentation to offset delivery time hurdles. Additionally, pressure data is required to inform bioreactor users of current process conditions.
Catalyst Evaluation Equipment
Catalyst development requires high temperature and pressure to prevent condensation of compounds and to analyze the chemical composition of exhaust gases from reactors. To find out under which conditions a catalyst has optimal performance for a particular chemical reaction, the high pressure range must be dealt with. In the application, the pressure must be accurately controlled and the pressure range is large. Also, the corresponding control device should be able to handle high pressure, high temperature and low flow. The product is perfectly adapted to the conditions in this application.
Gas Flow Control Applications in Analytical Instruments
A common factor in many analytical applications is the need for a small steady gas flow (flow range: 1-1000 sccm), since the gas flow and its changes are directly visible in the measurement, a stable gas flow is important. In analytical equipment, the carrier gas flow directly affects the measurement results. For example, the retention time of a substance in a chromatographic column depends directly on the stability of the fluid. When the flow fluctuates, so does the measurement. This product has short-term and long-term control stability.