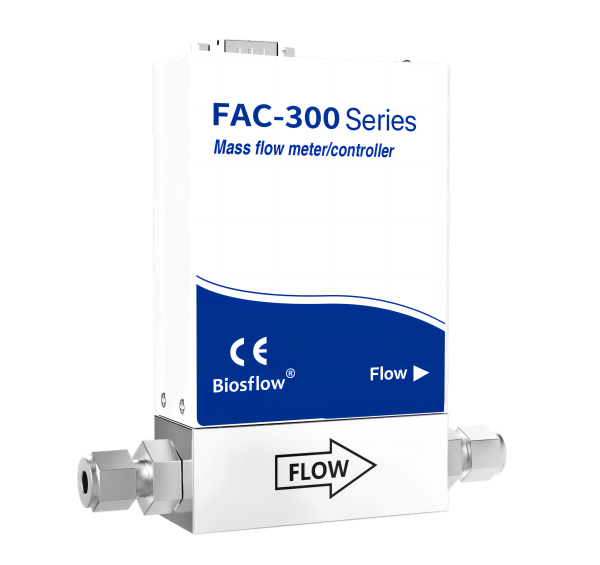
FAC 300 Analog Series Mass flow Controller and Meters
- Full Scale Flow Range: 10sccm-30slm
- Maximum Pressure Rating: 500Psi / 30Bar
- Repeatability: ±0.2% F.S
- Control Range: 2%~100% F.S
- Response Time: <2s
- Operating Temperature:0~50℃
- Analog Communication:0~5 V / 4~20mA
Description of FAC-300 Analog Series Mass flow Controller and Meters
The FAC series adopts a capillary thermal temperature difference sensor, and the measurement accuracy is not affected by temperature and pressure. The substrate is made of 316L stainless steel, which is suitable for toxic and corrosive gases, and the maximum working pressure can reach 750 Psi. Industry-leading long-term stability, precision backed by superior metrology systems and methods utilizing primary calibration systems to international standards, and a wide variety of analog I/O options. The FAC series has passed CE and Rohs certification and is the best solution for low-cost applications.
Biosflows FAC-320 Analog Mass Flow Controller and Meters Principle
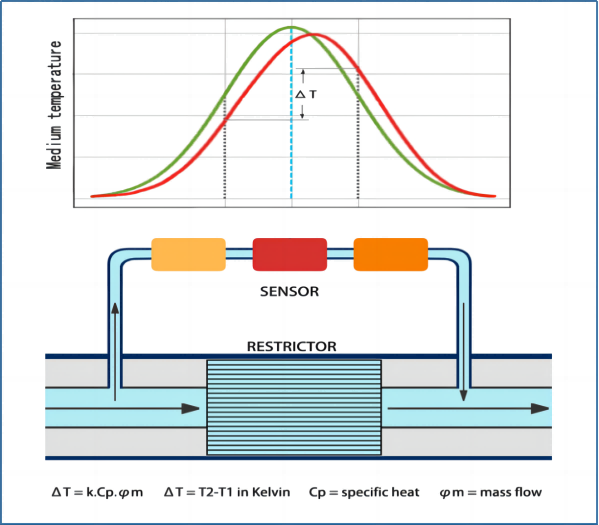
Sensor Schematic
The core sensor of the thermal mass flow meter (MFM) is the principle of capillary thermal temperature difference, which is composed of a stainless steel capillary with a thermal sensor and a heating element. A part of the gas flows through the bypass sensor and is heated by the heating element. The gas flow causes an asymmetrical temperature distribution, which is proportional to the mass flow through the sensor.
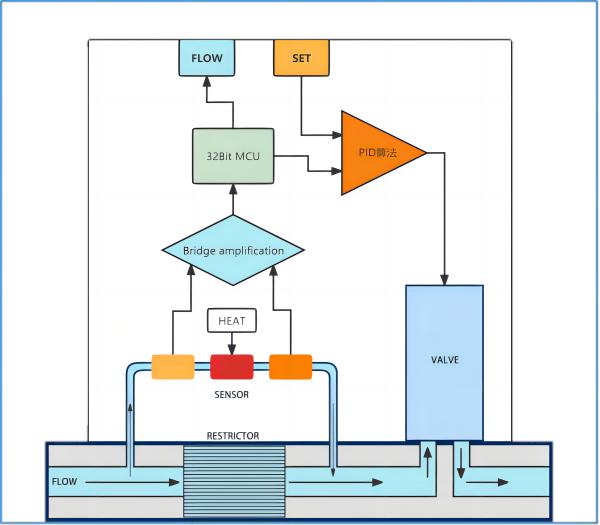
MFC Structure Diagram
The main flow channel of the thermal mass flow controller (MFC) is perfectly shunted by the laminar flow element, so that the output of the sensor has a linear relationship with the total mass flow. The output signal of the sensor is amplified and compared with the signal set by the user, the opening of the solenoid valve is controlled by the PID algorithm, the flow is adjusted, and the closed-loop control of the mass flow is realized.
Biosflows FAC-300 Analog Series Massflow Controller and Meters Technical Parameters
Performance | |
---|---|
Flow Accuracy | ±0.8% R.D and±0.2% F.S; ±1% R.D and ±0.5% F.S(>100 SLM) |
Repeatability | ±0.2% F.S |
Control Range | 1~100% F.S |
Response Time | <1s |
Temperature Coefficient | Zero: <0.05% of F.S./℃. Span: <0.1% of S.P. /℃ |
Pressure Coefficient | 0.2% of S.P. / Bar |
Operating Temperature | 0~50℃ |
Leak Rate | 1x10-9 atm. cc/sec He |
Preheat Time | 5 min accuracy to ±2% F.S (30 min to achieve the best accuracy) |
Power Supply | +15~24 V DC |
Maximum Power Consumption | 10W (MFC); 3W (MFM) |
Digital Communication | RS-485(Modbus Rtu protocol) |
Analog Communication | 0~5 V / 4~20mA |
Electrical Interface | 9-Pin D-connector (Male) |
Valve Type | Normally closed (MFM meaningless) |
Substrate Material | 316L stainless steel |
Sealing Material | Fluorine rubber, EPDM rubber, nitrile rubber |
Process connections | Tube/VCR Fittings |
FAC-300 Analog Series Massflow Controller and Meters Size and Weight
Model | A | B | C | D | H | E | F | G | M | Weight |
---|---|---|---|---|---|---|---|---|---|---|
FAC-320/1 | 76 | 124 | 13 | 31 | 125 | 56 | 17 | 10 | M4 | 0.6 |
Features of FAC-300 Analog Series Mass flow Controller and Meters
Long-term Stability and Accuracy
Long-term zero-point stability with less than 0.2% of full-scale variation per year; excellent signal-to-noise ratio performance for high accuracy at low setpoints, and excellent long-term stability through improved sensor manufacturing and burn-in testing processes.
Respond Quickly to User Setting
The combination of capillary chip sensor technology with frictionless valve technology and electronic technology enables the product according to customer’s command to respond quickly to command changes and overshoot (negligible undershoot).
Resistant to Toxic and Corrosive Gases
The capillary thermal temperature difference sensor effectively isolates the erosion of corrosive gases. The substrate of FAC-300 Massflow Controller is made of 316L stainless steel, and the chemical corrosion-resistant valve has super adaptability to toxic and corrosive gases.
Easy to Install and Use
The detachable flow sensor is used, so there is no need for monitoring and readjustment of the air pressure, and it is not affected by the installation angle. Since the analog quantity is only input/output, it is compatible with other MFC in terms of mechanical and electrical design.
Application of FAC-300 Analog Series Mass flow Controller and Meters
Plasma Equipment Gas Control Applications
The plasma section requires accurate, repeatable gas flow, while the optical section requires a reproducible purge gas flow. Furthermore, the gas delivery device needs to be compact and preferably as low cost as possible. Mass flow controllers produce accurate and repeatable flow in the range of 1.5 SLM to 20 SLM. Accuracy is essential for the contents of the reactor to have the correct composition. Welcome to Inquiry in Biosflow to get free quotation.
Gas supply system in brewing process
Before any type of flow control solution, the process was limited to controlling the flow of oxygen into the system by opening a valve and then timing the flow of oxygen into the brewing vessel. This rough estimate can lead to inconsistent beer quality from batch to batch. Using mass flow controllers to deliver exactly the required amount of oxygen into the brewing vessel, this solution improves the product quality and further reduces wasted manual excess oxygen and the cost of cleaning and sampling time.
Application of diamond preparation process
One of the common methods used for the production of diamond thin films is the hot wire vapor deposition technique, with mass flow controllers to ensure proper gas volume and process repeatability; since the flammability and explosiveness of process gases are safety concerns and must be closely controlled and monitored. Thermal mass flow controllers play an integral role in these applications or any other growth process involving vapor-phase grown diamond.